MEMS Sensors
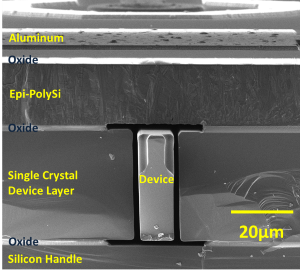
Micro Electro Mechanical Systems (MEMS) are sub millimeter-scale devices manufactured with the same materials and processes as semiconductor circuits. The Stanford Micro Structures and Sensors Laboratory works designing, fabricating and testing MEMS sensors for various applications including high performance inertial sensors, timing references, and others. The group developed and now specializes in the epitaxial encapsulation (epi-seal) process for MEMS devices.
The epi-seal encapsulation process provides an environment free of contamination that is crucial in allowing high performance and unrivaled stability. The pure silicon devices are manufactured at the Stanford Nanofabrication Facility (SNF) with feature sizes from tens of nanometers to hundreds of microns, and are monolithically encapsulated with silicon and silicon dioxide at the wafer level.
My research focuses on developing and testing a MEMS based oscillator that is more precise, smaller and requires much less power than a quartz oscillator. My work involves iterative design process of MEMS resonators and testing using devices such as amplifiers and other circuitry to test for the stability of our devices.
Micro-Ovenized Clocks
In this work, we demonstrate a novel dual-mode clock with an in-chip device layer micro-oven which operates at 10X reduced power consumption and provides more than 30X improved stability when compared to a recent result with a micro-oven embedded in the cap [2]. The decrease in the thermal time constant and in the micro-oven power dissipation improves compensation for ambient temperature variations and allows for significant improvements in the stability. This device layer micro-oven enables correction for ambient temperature fluctuations and achieves long-term stability over temperature in ppb, which is better than the stability of TCXOs and competes with state-of-the-art OCXOs, while requiring much less power.

Figure 1. Schematic of resonator structure. The two resonator modes used in the clock are shown.
Figure 1. Schematic of resonator structure. The two resonator modes used in the clock are shown.

Figure 2. Three dimensional rendering of encapsulated device shows all the encapsulation layers including inplane electrodes to sense movement in the device layer and top electrode to sense movement out-of-plane.
Figure 2. Three dimensional rendering of encapsulated device shows all the encapsulation layers including inplane electrodes to sense movement in the device layer and top electrode to sense movement out-of-plane.

Figure 3. Schematic of experimental set up: a phase locked loop was used to simultaneously track the frequencies of two modes in one resonator. A PI controller was used to control the micro-oven voltage and maintain a constant turnover temperature of 80 degrees Celcius.

Figure 4. Mean frequency error of 2nd order Lamé-mode at steady state with changes in ambient temperature.

Figure 5. Comparison of clock stability over temperature (-40 oC to 80 oC) for range of devices shows that the dual Lamé-mode clock (starred) has better stability and power consumption than leading TCXOs and OXCOs used in industrial applications.
These results demonstrate more than 30X improvement in the stability of a dual Lamé-mode clock and 10X reduction in the power consumption. This shows that stiff Lame-mode bulk resonators are ideal candidates for ultra-precise ovenized clocks since they are less susceptible to thermal expansion nonlinearities. Our results for temperature and long-term stability are the best of any previously- published or commercially produced MEMS-based clock, while also operating with heater power far below any conventional quartz OCXO. These devices have the potential to revolutionize applications that require ultra-stable references and low power.
To learn more, visit our lab page.
Thermal Effects of Ovenization on IMU Devices
In this work, we demonstrate the thermal effects of micro-ovenized clocks embedded in the device layer of a vacuum sealed MEMS inertial measurement unit. We demonstrate a novel in-plane suspension and heater that provides improved thermal isolation within a mm-scale chip, compared to in-cap heaters. We show the interaction of three resonators within a single die: an ovenized tuning fork, a resonant accelerometer, and a disk resonating gyroscope. We demonstrate that a device layer micro-oven, which operates at a tenth of the power of an encapsulation cap-layer micro-oven, has very small effects on the frequency of the other resonators in the die, thus proving good thermal isolation in our structures. We show that the in-plane heater isolation provides more than a 15X reduction of frequency deviation of adjacent sensors.

Figure 6. IR image of ovenized clock with inplane heater while heating to a power of 71 mW (left), IR image of ovenized clock with in-cap heater resonator while heating to a power of 159.2 mW (right).

Figure 7. Experimental set up: a phase lock amplifier was used to collect open loop sweeps of two devices at a time while applying a heating voltage at the terminals of the ovenized clocks.

Figure 8. Frequency shift in each device with changes in micro-oven power required to heat element to 70C.
This work demonstrates that in-plane micro-oven can provide more than 10X reduction of heating of adjacent sensors when compared with in-cap layer micro-ovens. Thus, proving that in-plane ovenization temperature compensation techniques can significantly improve the overall operation of single-chip IMU/Clock systems with lower required power and fewer thermal effects on adjacent non-ovenized devices.
To learn more, visit our lab page.